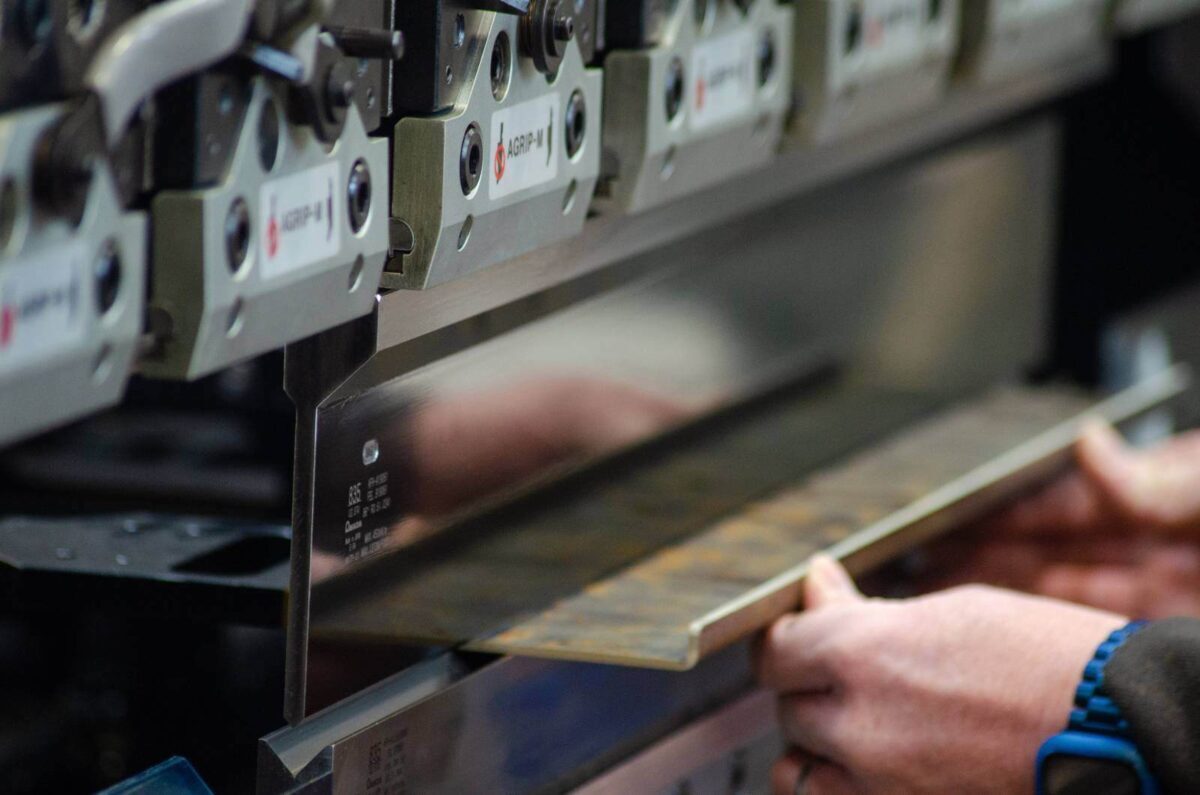
When evaluating contract manufacturing partners, many OEMs overlook a key capability—hydraulic press brake forming. Choosing a contract manufacturer with in-house hydraulic press brake capabilities can significantly improve production efficiency, precision, and cost control. In this article, we’ll explore the top reasons why hydraulic press brake services should be a key factor in your decision-making process.
What Is Hydraulic Press Brake Forming?
Hydraulic press brakes are machines used to bend and form sheet metal with consistent force. This technology is essential for producing precise bends in metal parts used across industries like aerospace, automotive, energy, and industrial equipment. Unlike manual methods or outsourcing, in-house forming with a hydraulic press brake ensures better quality control and faster turnaround.
Want a deeper look at how hydraulic press brakes work? Check out this overview from The Fabricator.
Benefits of Working with a Contract Manufacturer That Offers Hydraulic Press Brake Capabilities
Precision Bending for Complex Parts
Hydraulic press brakes offer superior accuracy. Contract manufacturers with this capability can form parts with tight tolerances and complex geometries—perfect for projects that demand high consistency and performance.
Faster Turnaround and Shorter Lead Times
In-house press brake services eliminate the need to ship parts to third-party vendors. This saves time, reduces logistical complexity, and shortens your production timeline.
Cost Savings Through Consolidated Services
Working with a single contract manufacturer that offers cutting, forming, and assembly under one roof minimizes overhead. It also helps reduce errors, communication delays, and shipping costs between separate vendors.
Improved Quality Control
With forming handled in-house, manufacturers can inspect each part immediately after bending. This leads to better defect detection and ensures components meet design specs before moving to the next stage.
Support for Custom and Small-Batch Projects
Hydraulic press brakes are flexible enough to support low-volume or custom part production. Whether you need a short run of brackets or a prototype with unique specs, a contract manufacturer with this capability can help you pivot quickly.
What to Look for in a Press Brake Partner
Not all press brake capabilities are equal. When choosing a contract manufacturer, look for:
- CNC press brake systems for automated precision
- Operators with metal forming experience
- The ability to handle a range of materials and thicknesses
- Integration with cutting and finishing services
At MSI, our 130-ton CNC press brake enables us to handle a wide range of custom forming needs—all backed by ISO 9001:2015 quality standards. Learn more about our key equipment here.
Industries That Benefit from Press Brake Capabilities
Across industries, hydraulic presses play a key role in helping technicians bend and assemble sheet metal, components, Aerospace – Precision brackets and enclosures
- Energy – Control panels and structural supports
- Industrial Equipment – Machine frames and guards
- Transportation – Chassis parts and mounting plates
For example, a manufacturer of commercial battery systems might rely on formed aluminum or steel enclosures to house sensitive components. With in-house press brake capabilities, we can bend those parts to spec with fast turnaround.
Why It Pays to Keep Press Brake Forming In-House
Choosing a contract manufacturer with hydraulic press brake capabilities gives OEMs greater control over quality, timing, and cost. It streamlines production and ensures that your metal parts meet exacting standards from start to finish.
Looking for a reliable partner with press brake forming expertise? Contact MSI today to request a quote or discuss your project.