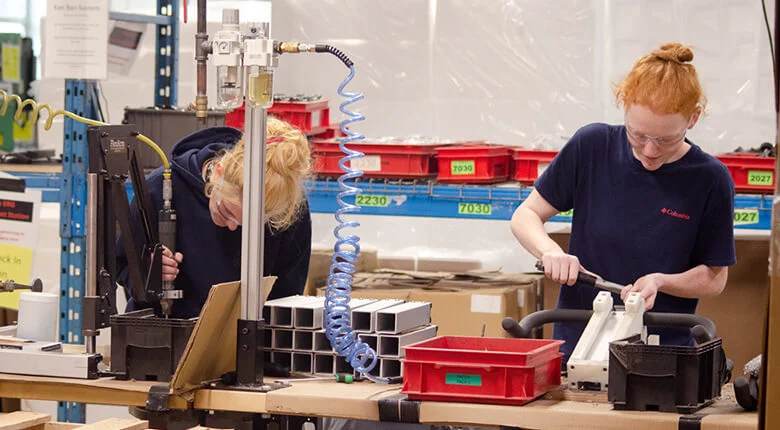
Choosing the right contract manufacturer committed to quality management is a strategic decision that directly impacts product quality, lead times, and customer satisfaction. For OEMs and businesses in regulated industries, quality management isn’t just a value add—it’s a requirement. This article explores the benefits of working with a partner who puts quality at the core of their operations.
What Is Quality Management in Contract Manufacturing?
Quality management refers to the systems, processes, and standards a manufacturer uses to ensure every product meets defined specifications. These systems often include ISO certifications, inspection checkpoints, documentation, and team training. A contract manufacturer with strong quality management practices builds reliability and trust into every stage of the production process.
Want to learn more about ISO 9001:2015 standards? Explore the official ISO website.
Benefits of Working with a Quality-Focused Contract Manufacturer
1. Improved Product Consistency
Manufacturers that follow standardized processes can produce parts that meet the same specifications every time. This consistency reduces the need for costly rework or late-stage adjustments.
2. Reduced Production Risk
By adhering to rigorous quality standards, contract manufacturers can identify and resolve issues before they impact timelines or customer satisfaction. This proactive approach helps prevent defects and minimizes downtime.
3. Stronger Compliance for Regulated Industries
Industries like aerospace, defense, and medical devices require strict adherence to quality protocols. A contract manufacturer committed to quality management is more likely to maintain the documentation and traceability needed for compliance.
4. Faster, More Reliable Lead Times
When processes are well-documented and repeatable, manufacturing runs become more predictable. That means fewer surprises, faster deliveries, and a smoother production timeline.
5. Confidence in Every Build
When your contract manufacturer has quality systems in place, you gain peace of mind. You can rely on their team to catch issues early and deliver parts that meet your expectations from the first unit to the last.
What to Look for in a Quality-Driven Partner
Not all manufacturers approach quality the same way. Look for these indicators when evaluating a partner:
- ISO 9001:2015 certification
- Quality assurance (QA) and quality control (QC) programs
- Documented inspection processes
- Continuous improvement initiatives
- In-house training for fabrication, assembly, and inspection teams
At MSI, quality is woven into every step of production. Explore our capabilities or contact us to learn how our quality-first approach supports your next project.
Quality Isn’t Optional—It’s a Competitive Advantage
Partnering with a contract manufacturer committed to quality management gives your business a measurable edge. You’ll gain faster lead times, more reliable products, and peace of mind knowing your project is in capable hands.