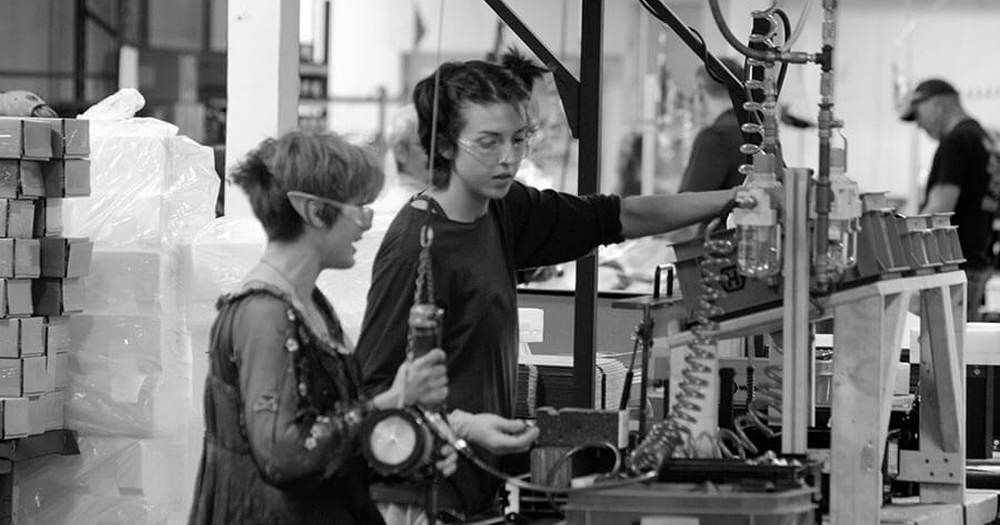
While lean manufacturing has typically been utilized by larger enterprises, small to medium-sized businesses (SMBs) and original equipment manufacturers (OEMs) are increasingly leveraging strategic partnerships with trusted contract assemblers to implement lean practices into their assembly processes. The lean manufacturing process has successfully differentiated itself from its conventional and outdated mass-production counterpart by clearly illustrating the extensive benefits it can offer businesses and OEMs.
While mass production methods emphasize increased total output for higher profit margins, lean contract assembly and sub-assembly services ensure a streamlined production process to reduce cycle time, increase production quality, and enhance customer satisfaction.
Benefits of Lean Contract Assembly and Sub-Assembly Services
Contract assembly service providers that adhere to lean manufacturing philosophies proactively strive for perfection and continually seek to optimize their production processes to better serve their customers. Outsourcing assembly projects to a trusted contract manufacturer that specializes in lean concepts will streamline and simplify assembly processes in order to reduce waste and unnecessary costs.
In addition to removing the 8 forms of waste from the assembly process, here are the top 3 benefits of leveraging a lean contract manufacturer for your assembly or sub-assembly project.
1. Better Quality Control
One of the core tenets of lean manufacturing is consistent quality control. Since lean manufacturing deemphasizes excessive production, there is more of an opportunity to focus on improving quality. Inefficient and inconsistent product quality can lead to wasted resources, lost time, and a damaged business reputation.
An experienced lean contract assembler will offer a guarantee on all finished products, and if a defect does occur, it should be quickly identified, corrected, and optimized to avoid future downtime. Contract assemblers that uphold lean principles leverage problem-solving techniques such as mistake-proofing to identify the root cause of the problem and prevent the mistake from reoccurring.
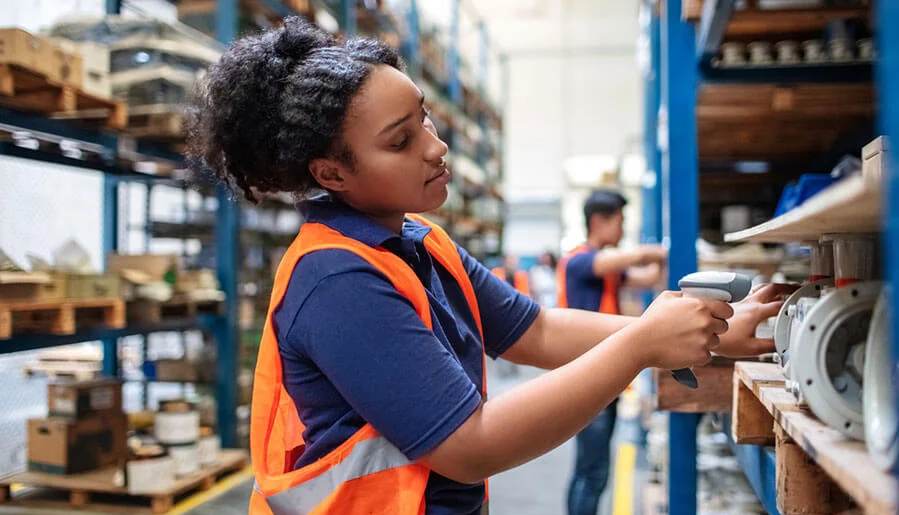
2. Reduced Lead Times
Lead times can be generally defined as the amount of time passed from the start of the process until completion. In manufacturing, lead times represent the time it takes to create a product and deliver it to an end-user. Businesses and OEMs seek to reduce lead times to streamline operations, improve productivity, and increase output and revenue. Businesses with long lead times risk negatively impacting their brand reputation and assembly process efficiency.
A contract manufacturer that adheres to lean manufacturing principles relentlessly prioritizes eliminating waste, and continuous improvements to enable businesses and OEMs to respond to customer demands quicker, with fewer delays to shorten production cycle time and ultimately reduce lead times. Prioritizing lead time reduction enables other positive effects such as:
- Improved customer satisfaction
- Decreased waste production
- Reduced labor
- An increased cash flow due to efficient and lower inventory levels.
3. Increased Profits
Lean production philosophy prioritizes the maximization of profit margins. Integrating lean production principles into assembly and sub-assembly projects increases performance efficiency with less waste and better quality, which drives consumer satisfaction, retention, and ultimately, revenue.
Businesses and OEMs should consider outsourcing assembly and sub-assembly services to lean manufacturers to reduce the amount of space needed for production, decrease labor spend, and reduce unnecessary raw material costs to maximize return on investment (ROI). With an increased flow of capital, businesses and OEMs have more opportunities to invest in company growth and scaling business-critical operations.
Partnering with a Lean Contract Manufacturer for Your Assembly Project
Lean manufacturing can be viewed as a successful business philosophy proven to reduce costs and eliminate waste, maintaining the highest levels of quality in order to meet customer expectations. A lean contract assembly service provider consistently looks to optimize production processes so you can get your product to market faster and successfully capitalize on market opportunities.
Businesses and manufacturers that partner with a qualified and experienced contract manufacturer that adheres to lean manufacturing principles will streamline their production process, improve efficiency, control costs, eliminate waste, and better position themselves for success over competitors.