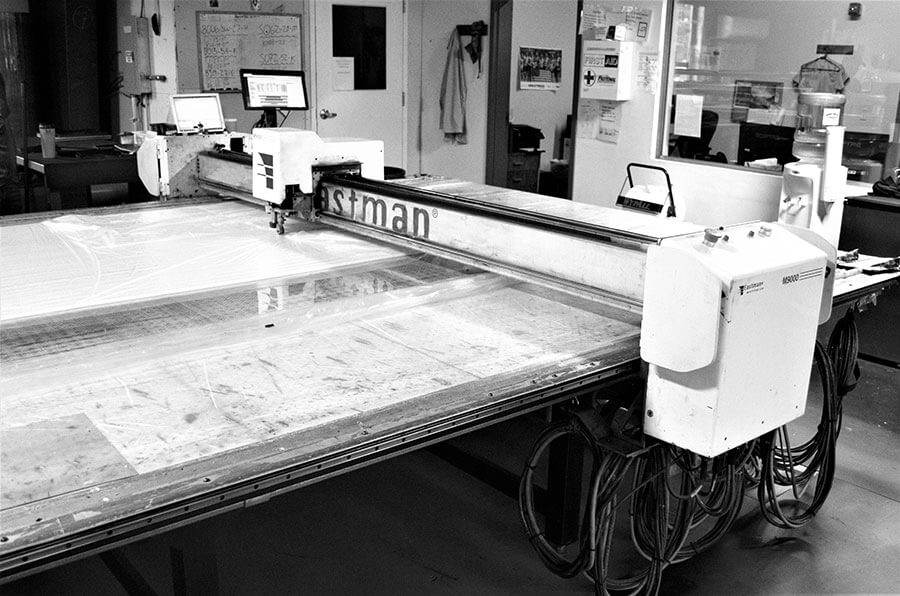
From complex shapes to one-off production runs, computer numerical control (CNC) static cutting table systems provide manufacturers a versatile and cost-effective cutting solution with superior advantages over manual cutting processes.
Original Equipment Manufacturers (OEMs) and businesses should understand what CNC cutting is and the benefits of using automated CNC static cutting tables so they can identify a contract manufacturer that has the resources and cutting capabilities to ensure their needs are met with pinpoint precision.
What is CNC Cutting?
CNC cutting, or CNC machining, is a widely used automated manufacturing process that utilizes computerized controls to operate and manipulate cutting tools such as drills, lathes, and mills to shape stock material into custom parts and designs without the need of a manual operator directly controlling the machine. CNC cutting relies on digital instructions made on Computed Aided Manufacturing (CAM) or Computed Aided Design (CAD) software.
Automated CNC cutting machines cut with accuracy, repeatability, and are available in a range of lengths and widths to accommodate a wide variety of designs. There are two main types of automated CNC cutting systems – static and conveyor – both with unique advantages and disadvantages depending on the cutting project. Static cutting tables are durable and easy to use, while conveyor cutting tables are generally more expensive, use complicated software, and require frequent maintenance.
At MSI, we have two Eastman M9000 static cutting tables that can cut thin layer films at a quarter-inch thickness, cut sheets up to 8 feet wide and 20 feet long, operate 24 hours a day, and cut virtually any material at speeds of up to 60 inches per second with an accuracy of +/- .030 inches. The Eastman M9000 static cutting table is capable of cutting materials including but not limited to cheesecloth, plastic, cotton, leather, nylon, and vinyl as well as more high-tech materials such as carbon fiber, p-tex, and fiberglass-polyester blends.
4 Advantages of Using Automated CNC Static Cutting Table Systems
Businesses that take advantage of automated CNC static cutting tables can leverage the technology to help them scale and achieve their precision cutting goals. From improved accuracy to lower costs, here are four advantages of using a contract cutting service that uses advanced CNC cutting tables like the Eastman M9000.
1. Enables Cost-Effective Cutting of Complex Shapes
Cutting complex shapes, no matter the production size, can be a time-consuming and labor-intensive process which is why a majority of OEMs and businesses outsource the cutting process to contract manufacturers.
While die-cutting machines have the capability to cut complex shapes, OEMs and businesses that have a smaller production run do not want to spend the money on designing a custom die which can cost anywhere between $1,000 – $10,000 depending on the complexity of the shape. OEMs and businesses that need complex shapes for smaller production runs can avoid costly custom dies by using CNC static cutting tables.
2. Improves Accuracy and Precision
One of the greatest benefits of contract cutting is improved accuracy. Advanced CNC static cutting tables can cut materials with an accuracy of +/- .030 inches, which is extremely hard to achieve and maintain using manual cutting processes. In some industries, the margin of error must be close to non-existent. CNC static cutting tables provide OEMs and businesses high-quality finished products that ensure customer satisfaction and the needed assurance that if their industry requires precise tolerances, they’re continuously meeting rigorous standards and regulatory compliance.
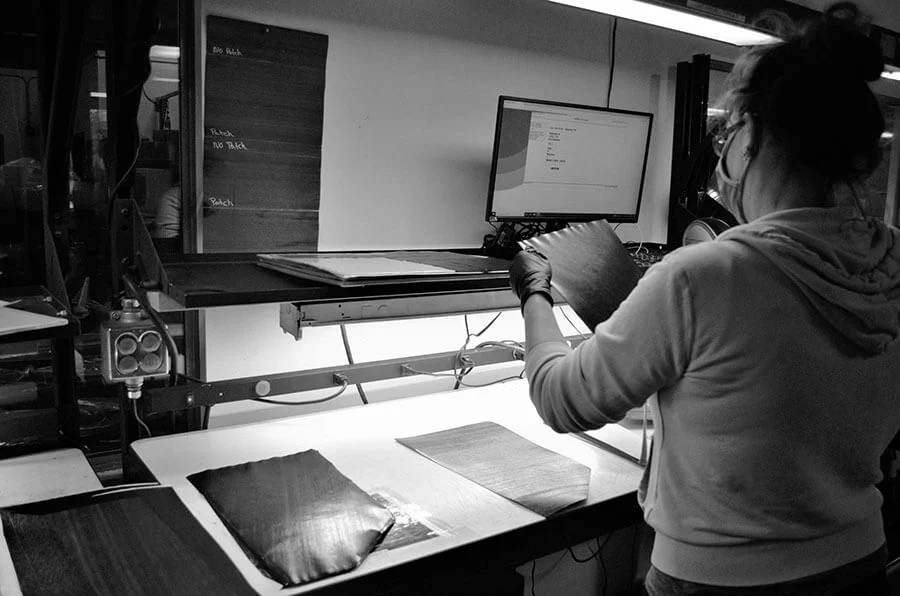
3. Ensures Repeatability and Scalability
One of the most valued benefits of CNC cutting is the repeatability of cutting materials. When OEMs and businesses need their products cut, it’s critical that every product is cut with the same quality and is identical to one another. If a company needs 100 complex patterns cut out of carbon fiber, all 100 need to be cut the same. This high level of consistency cannot be achieved using a manual cutting process.
However, design parameters and specifications can be digitally entered into a CNC static cutting machine’s software to ensure consistency one cut after another, affording OEMs and businesses flexible scalability.
4. Increases Productivity
Conventional manual cutting produces inefficiencies and is prone to human error that results in cutting jobs taking longer than they need. A CNC cutting machine enables greater productivity by making cuts faster and more accurately. A CNC static cutting table programmed with the latest CAD software can move more efficiently and reduce unnecessary movements leading to a more streamlined cutting process. In a highly competitive manufacturing environment, productivity is the key to unlocking greater profitability. A contract manufacturer that utilizes automated high-speed machining can complete cutting projects quicker and enable OEMs and businesses to increase their order capacities to meet the growing demands of their customers.
Maximize Productivity with a Reliable Contract Cutting Service
Whether it be for a single one-off job or a complete production run, automated static cutting tables enable facilities to maximize productivity, increase material utilization, and reduce labor costs. Businesses and OEMs that choose to partner with an experienced contract manufacturer that has static cutting table systems eliminate the inefficiencies of conventional manual cutting and replace them with the pinpoint accuracy of CNC machining.
Large up-front investments into advanced cutting machines can limit business growth potential. By choosing a reliable contract cutting service that offers CNC cutting, you solidify a hassle-free production process that’s quick, accurate, cost-effective, and scalable.