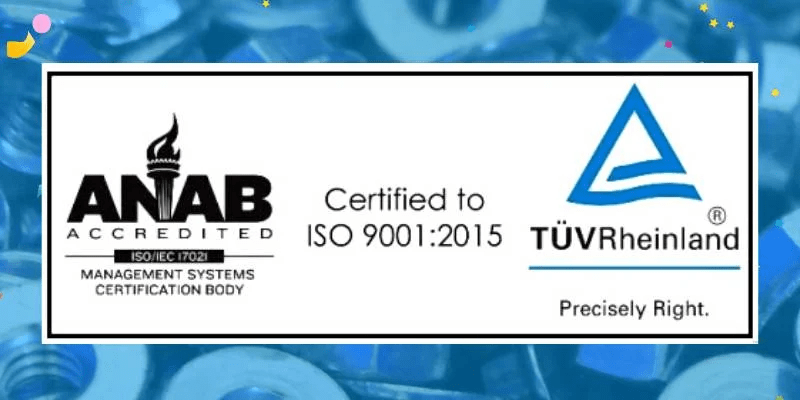
We are thrilled to be celebrating another ISO 9001:2015 recertification of our quality management systems that apply to manufacturing, assembly, precision cutting, and fabrication. Our commitment to delivering high-quality products and services is unwavering, and this recertification is a testament to our dedication. We are proud of our team’s hard work and would like to thank them for their efforts in achieving this milestone. Go team MSI!