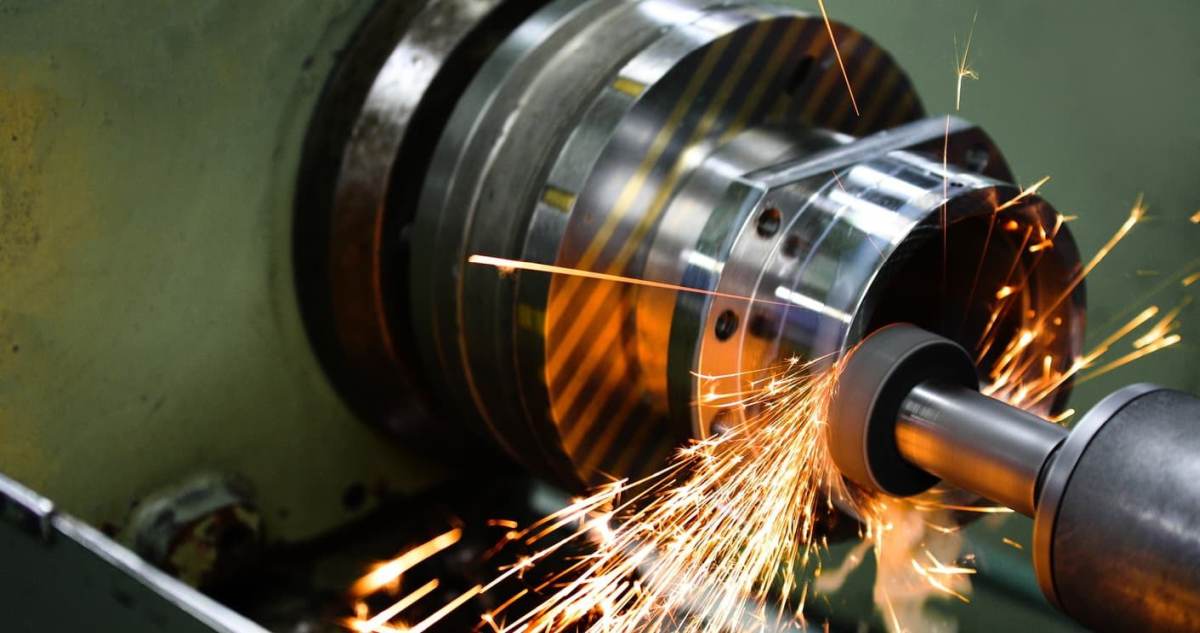
Complete Guide to Metal Finishing Processes for Fabricated Parts
Enhancing Durability, Appearance, and Performance in Metal Fabrication
Metal finishing is the final—and crucial—step in the manufacturing process. It alters the surface of fabricated metal components to improve their durability, aesthetic appeal, and resistance to corrosion and environmental damage. For precision sheet metal fabrication, finishing is what takes a raw part and turns it into a ready-to-install solution.
At Manufacturing Solutions Inc. (MSI), our in-house metal finishing capabilities support high-quality outcomes across industries including aerospace, defense, energy, and industrial equipment. Whether it’s powder coating, phosphate coating, or abrasive blasting, our vertically integrated facility ensures faster lead times and better quality control.
Types of Metal Finishing Techniques
Metal finishing techniques fall into two main categories:
- Adding or Altering Finishes – Applying coatings or chemical treatments to enhance properties.
- Removing or Reshaping Finishes – Modifying surface texture by cleaning, polishing, or blasting.
Selecting the right finish depends on product function, environment, material, and desired aesthetics. Let’s break down each of these categories to ensure that businesses select a metal finishing process that fits their needs. Businesses that take the time to learn the different types of metal finishing techniques will save time, money, and labor.
Adding and Altering Metal Finishing Processes
These techniques enhance corrosion resistance, electrical conductivity, and surface appearance by applying a new layer or altering the chemical composition of the surface.
There are many processes, but some of the most common are electroplating, electroless plating, passivation, hot blackening, and powder coating.
Electroplating
Electroplating, i.e., electrodeposition, is a process that involves the deposit of a metal or metal alloy onto the surface of a metal part. The process uses a substrate material that is typically a lighter and lower-cost material and encapsulates it in a thin shell of metal, such as copper or nickel. Manufacturers can electroplate a single metal onto an object or a combination of metals. Manufacturers tend to layer multiple metals to maximize strength and conductivity. Some materials commonly used in electroplating include but are not limited to:
- Brass
- Copper
- Gold
- Iron
- Nickel
- Silver
- Titanium
- Zinc
Electroless Plating
Electroless plating, also known as chemical plating or auto-catalytic plating, is a metal processing technique that plates metal chemically rather than by electrical means. The electroless plating process involves the deposition of metals including nickel, silver, gold, and copper on the surface of a variety of materials using a reducing chemical bath, creating a catalytic reduction of metal ions to plate the part without any electrical energy dispersal.
Unlike electroplating, electroless plating is a chemical process that doesn’t require any extra machines or electrical power. Electroless plating offers several technical advantages including, but not limited to:
- Creates an even layer of metal
- Does not require advanced jigs or racks
- Flexibility in plating thickness and volume
- Achieves bright, semi-bright, and matte finishes
Passivation
Typically leveraged as a post-treatment plating process, passivation is a chemical treatment predominately for stainless steel and other metal alloys like aluminum that enhances the ability of the treated surfaces to resist corrosion and reduce the impact of environmental factors such as water or air. During the passivation process, a thick protective metal oxide coating is applied to slow down the oxidation process, which doesn’t typically alter the appearance of the material.
Some of the benefits of passivation include but are not limited to:
- Increased corrosion resistance
- Reduced maintenance
- Removed contamination
Hot Blackening
Hot blackening is a metal finishing process that applies a thin black oxide coating to the surface of a substrate. This technique utilizes a series of tanks containing various cleaning agents, coolants, and caustic materials and is typically performed in large batches, resulting in a process ideally suited for smaller parts.
Manufacturers typically leverage hot blackening to increase the abrasion resistance of metal parts and provide a black matte finish on automotive parts, firearms, and military applications where a protective dark coating is required.
Powder Coating (Available In-House at MSI)
Instead of using a liquid to coat a metal product, powder coating is a metal finishing process that involves the application of a dry powder. During the powder coating process, a variety of ingredients including, pigments, curatives, flow modifiers, leveling agents, and other additives are combined to create the dry powder coating. Once the powder is created, it is electrostatically deposited onto the surface of the substrate and placed in a specially designed oven to produce long molecular chains, resulting in high cross-link density.
Powder coatings generally provide a more durable finish than liquid paints while still providing an attractive finish. Powder coated metal products are more resistant to diminished coating quality as a result of chemicals, moisture, ultraviolet light, and other extreme weather conditions. MSI offers in-house powder coating with quick turnaround and quality consistency across production runs.
Phosphate Coating (Available In-House at MSI)
Phosphate coating, also referred to as phosphatization, refers to a chemical treatment that is commonly applied to steel parts and other metals including cast iron to create a thin adhering layer that provides strong adhesion and increases corrosion protection. The thin adhering layer of phosphate coating is typically composed of iron, zinc, or manganese phosphates. It is important to note the finish provided by phosphate coating creates a gray to black appearance.
In addition to increasing corrosion protection, phosphate coating prolongs the lifespan of organic coatings, provides a suitable base for lubricants, and is used as a pretreatment for subsequent coatings such as paint or powder coating. Phosphate coating can be paired with oil coating processes to enhance the rusting and anti-galling properties of the metal part. MSI provides this in-house as part of our fully integrated finishing solutions.
Removing and Reshaping Metal Finishing Processes
Removing and reshaping metal finishing techniques are used to alter the surface of a part or product to attain the desired finish by removing or reshaping it. These metal finishing processes are used when the end-user desires a polished, reshaped, abrasive, or aesthetically pleasing finished metal part or product.
There are various processes to remove/reshape a part’s surface, but some of the most common methods are electropolishing, buff polishing, and abrasive blasting.
Electropolishing
Electropolishing leverages an electric current to remove metal ions from a metal part, typically stainless steel or similar alloys, to create a smooth, shiny, and streamlined surface texture. The benefits of electropolishing include but are not limited to:
- Improves corrosion resistance
- Decreases cleaning time
- Removes burrs and small amounts of debris
- Eliminates peaks and valleys
- Polishes hard-to-reach areas
- Reduces the size of metal parts in some instances
Buff Polishing (Available In-House at MSI)
Similar to electropolishing, buff polishing is a metal finishing process used to clean and smooth the surface of a metal part. The main difference between the two processes is that buff polishing doesn’t require any type of electrochemical reaction and instead uses a machine equipped with a cloth wheel. Manufacturers commonly leverage buff polishing to provide a glossy, decorative, and visually appealing finishing to their metallic components and products. Buff polishing is also used to prepare metal parts for electropolishing.
Abrasive Blasting (Available In-House at MSI)
Abrasive blasting is a metal finishing process that uses high-pressure propulsion to forcibly propel a stream of abrasive material against the surface of a metal part. This process is leveraged to combine surface finishing and cleaning into one process to save money and time and can also be used as a surface preparation treatment prior to painting, coating, or plating.
It is important to note there are several variations of this process, each using different abrasive materials. The most common abrasive blasting processes are shot blasting which uses metal shot such as aluminum oxide or carbon grit and sandblasting which uses sand.
The benefits of abrasive blasting include but are not limited to:
- Removes surface contaminants
- Produces a smooth and clean finish
- Alters the shape or increases the surface area
- Provides surface preparation treatment prior to plating, painting, or coating
Additional Industrial Metal Finishing Options
In addition to MSI’s in-house finishing methods, other specialty processes are often used in aerospace, defense, and medical industries:
- Electropolishing & Hot Blackening – Common in sectors requiring specific finishes or precision tolerances.
- Spray Painting – Offers color variety and flexibility for small-batch projects.
- Vibratory Bowl Finishing (Available In-House at MSI) – Smooths and deburrs parts efficiently, ideal for batch processing.
Choosing the Right Metal Finishing Method
When selecting a finishing method for sheet metal parts or assemblies, consider:
- End-use environment (corrosive, high-wear, or outdoor use)
- Material compatibility
- Aesthetic expectations
- Adhesion requirements for secondary finishes
- Regulatory compliance for defense or aerospace applications
At MSI, we help OEMs and manufacturers optimize their projects from cutting to coating. Explore our metal fabrication capabilities and let’s talk about how we can support your finishing and fabrication needs.