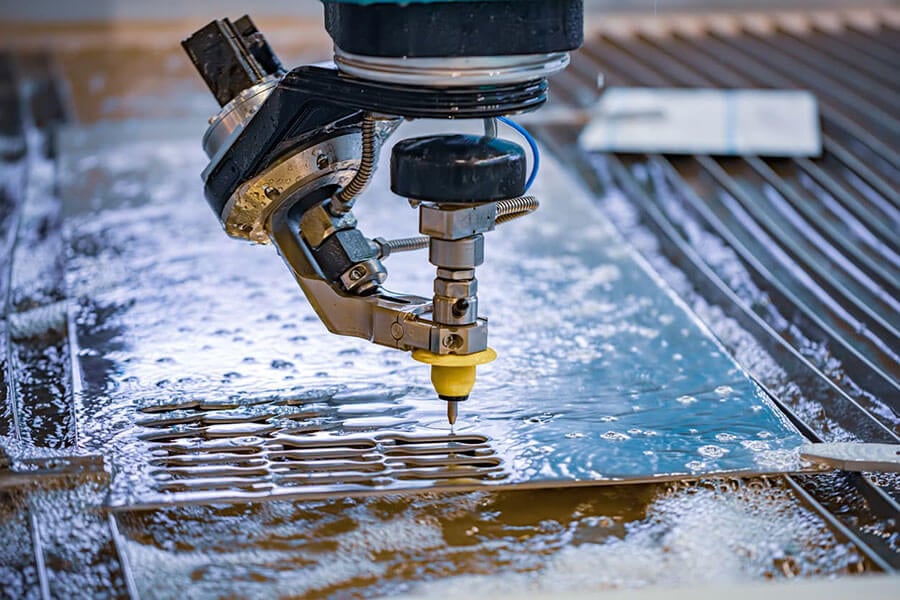
No matter what the specific precision cutting needs are, whether a company needs high-tech materials such as carbon fiber or efficiently cut fabrics for garments or housewares, the necessity for highly-accurate cuts with microscopic tolerances remain the same. Continue reading to find out more about the benefits of using waterjet technology for precision cutting.
Industries such as aerospace, automotive, and medical are examples of the many industries that rely on extremely precise custom cutting to provide high-quality results while maintaining regulatory compliance. The waterjet cutting process offers manufacturers the flexibility that no other cutting process can offer: the ability to efficiently cut virtually any material with unparalleled accuracy. Flexibility is just one of the many benefits waterjet cutting has to offer.
The global waterjet cutting machine market size is expected to grow at a compound annual growth rate (CAGR) of 5.1% from 2020 to 2027, and for good reason. The versatility of cutting materials and the need for a more environmentally-friendly custom cutting process in industries such as automotive and mining are key factors attributing to the increased popularity and projected market size of waterjet cutting machines.
Businesses should familiarize themselves with the benefits of a waterjet cutter so they can successfully identify and choose the right contract manufacturer that is aligned to meet and exceed their custom cutting needs.
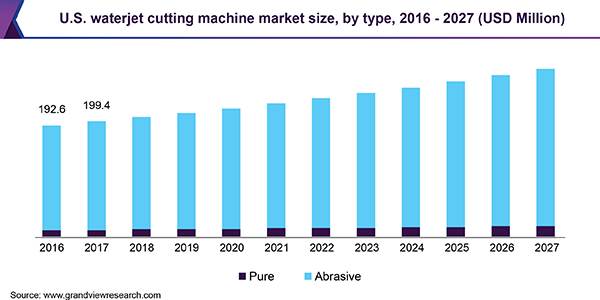
Advantages of Using Waterjet Cutting for Custom Cutting Projects
Businesses should take advantage of the benefits of using a waterjet cutter and how the process can help them scale and achieve their precision cutting goals. Companies should be aware of a prospective precision cutting provider’s capabilities and resources and if they offer waterjet cutting. Businesses should also be familiar with the required documentation and information that is needed to get the precision cutting service underway.
Here is an in-depth look at the benefits of using waterjet cutting technology.
Range of Materials
The diversity of materials that can be cut with a waterjet cutter is one of the most attractive capabilities of this technology. Waterjet cutting processes can cut different materials based on strength, durability, corrosion resistance, and conductivity including:
- Metals – Waterjet cutters are capable of cutting all types of metals including hardened tool steel, aluminum, titanium, carbon steel, stainless steel, and red metals (copper, brass, and bronze).
- Naturals – Waterjet cutting machines use specialized techniques such as low-pressure pierce, water-only cutting, and vacuum assistance to cut a wide array of natural materials including glass, stone, wood, leather, and ceramics.
- Composites – Waterjet cutters precisely cut any fiber-reinforced material, including carbon fiber, fiberglass, and Kevlar reinforced personnel armor. Waterjet cutters are able to quickly and cleanly cut composites without the drawbacks that come with conventional machining such as tooling changes and restrictions due to heat buildup.
- Plastics & Rubber – Waterjet cutting allows for efficient and precise cutting of plastic and rubber materials such as foam, rubber, linoleum, Plexiglas, polycarbonates, and acrylic. Businesses that use waterjet cutting can navigate around the material distortion barrier that is often encountered while machining plastic on conventional Computer Numerical Control (CNC) machines by using the cold cutting method of a waterjet cutter.
Thickness and Shape Cutting Capabilities
In addition to the type of materials that can be cut, a waterjet cutter is not limited by the material thickness. Waterjet cutters create a needle-thin cutting stream which can cut almost any shape and thickness, eliminating the need for additional machinery. This in turn reduces manufacturing costs and the amount of space needed.
The ability to cut materials and composites varying in thickness will ensure regulatory compliance in industries that require advanced cutting processes. While other cutting techniques may start to lose performance quality when cutting thicker materials, a waterjet cutter maintains reliable precision.
Cost-Effectiveness
Compared to traditional cutting methods, waterjet cutting is more cost effective because of the minimized cost of fixturing and tooling. Additionally, waterjet cutting is able to make products quicker and with less excess materials, which also contributes to a much more cost-effective product.
Waterjet cutting also eliminates the need for edge cleanup, which makes the parts ready to use immediately, reducing labor costs and increasing productivity. This significantly accelerates the custom cutting process and saves time, contributing to an overall increase in efficiency.
Variety of Waterjet Cutting Methods
There are a variety of cutting methods associated with waterjet machines that businesses can leverage depending on their particular precision cutting needs.
- Pure Water Cutting – Pure water cutting is most suitable for cutting soft materials such as food, foams, papers, or plastics. The process is extraordinarily environmentally friendly because its main byproduct is pure, recyclable water.
- Abrasive Water Cutting – Abrasive water cutting is defined by the mixing of a hard, powdery material into the water jet such as garnet or corundum to act as an abrasive agent. This process is more suitable for hard materials such as metal, marble, and composites.
- Low-Pressure Pierce – This waterjet cutting method helps prevent material from cracking by operating on low pressure. This process is more suitable for brittle materials like glass, stone, and ceramics.
- Wiggle or Dwell Piercing – Wiggle piercing, also referred to as dwell piercing, is a method in which water jet streams move repetitively across a very short distance to precisely cut the material. This process is suitable for making holes in thick materials.
Superior Edge Quality
Cutting with a waterjet produces a smooth edge with no burn marks, cracking, or excess burrs. Since waterjet cutting is a cold cutting method, there are no heat-affected zones which can cause a change to the molecular composition decreasing the tensile strength of the material. In many cases, waterjet cutting also eliminates the need for secondary finishing which creates significant time savings and improves efficiency. The capability to provide superior edge quality is paramount for businesses that prefer water-only processes such as the automotive and defense industry.
Next-Generation Precision
When it comes to precision cutting, the margin of error must be close to non-existent. Standard waterjet cutters use nearly 60,000 PSI when cutting, which significantly reduces the already exceptionally small margin of error associated with traditional precision cutters. The most common industries that benefit from the increased precision cutting capabilities of waterjet cutters are the food, aerospace, military, and automotive industries.
Low Environmental Impact
Waterjet technology only uses natural resources such as water and sand to reduce the harmful environmental impacts of the cutting process. There’s no air pollution and no exposure to potentially harmful toxins. Operators of the waterjet machines, as well as the end-user, are protected since no chemicals, heat, noxious fumes, liquids, or oils are used in, or caused by, the waterjet precision cutting process.
Using Waterjet Cutting For Your Precision Cutting Needs
Waterjet cutting is an extremely versatile precision cutting service that can be used in a wide variety of industries for intricate designs, and precision cutting jobs that require high tolerances.
Businesses no longer need to worry about meeting the rigorous standards found in industries that require precise tolerances. Waterjet cutting ensures maintained precision for nearly any material with an exceedingly small margin of error.
By choosing to partner with a qualified and trusted precision cutting service provider that offers waterjet precision cutting services ensures your cutting needs will be met with pinpoint precision using a cost-effective, scalable, and environmentally friendly process.