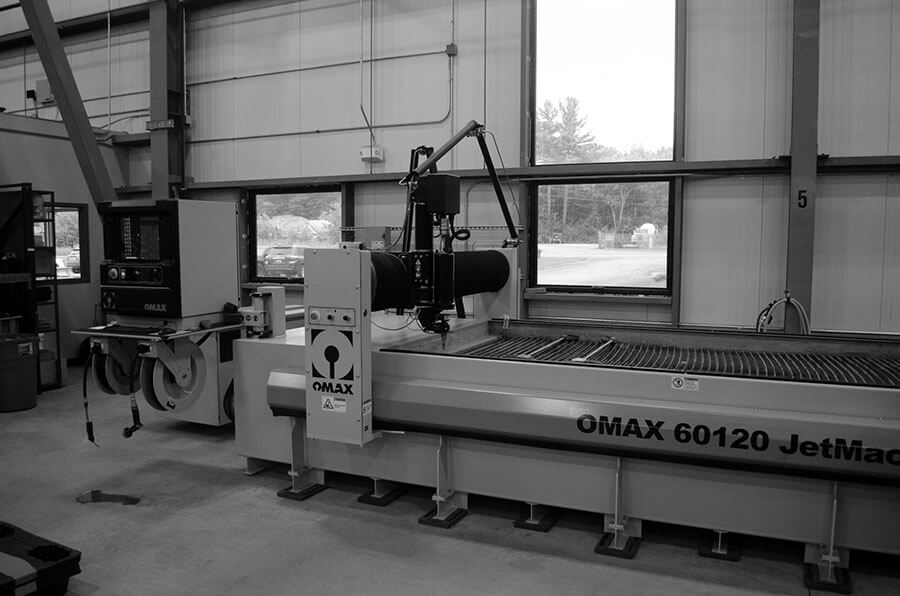
Whether your company needs to cut high-tech materials such as carbon fiber or efficiently cut strong materials such as steel and aluminum, your contract manufacturing partner will need the right precision cutting equipment to complete your production run efficiently and with pinpoint precision.
OEMs and businesses that partner with a precision cutting service provider with multiple advanced cutting tables that specialize in different cutting methods, such as waterjet cutters and automated static cutting tables, will ensure their precision cutting project is completed as fast as possible with the highest degree of accuracy at the most cost-effective price.
For the purpose of this blog, we’ll be comparing the OMAX 60120 JetMachining® Center and the Eastman M9000 static cutting table as these are specific cutting tables available for customers to utilize as part of MSI’s precision cutting services.
Let’s break down the unique advantages of waterjet cutting and automated static cutting to get a better understanding of how these two advanced precision cutting processes complement each other.
Waterjet Cutting Tables
Waterjet cutting is a versatile precision cutting method that can be used in a wide variety of industries for intricate designs and precision cutting jobs that require consistently tight tolerances. Waterjet cutting tables have a fast-set up time and can cut a wide range of materials without Heat Affected Zone (HAZ) or leaving heat-hardened edges. Due to fast programming and set-up times, waterjet cutting tables are great for creating prototypes and for short-run precision cutting projects.
From precision to variety of materials, here are just a couple of the many beneficial reasons to choose waterjet cutting for your next project.
Materials – Waterjet cutting tables can cut a range of materials, however since most fabric cutters don’t want their materials to get wet, waterjet cutting isn’t the best cutting process for fabrics. Waterjet cutters excel at cutting different materials based on strength, durability, corrosion resistance, and conductivity including metals, natural materials, composites, and plastics.
Thickness – Abrasive waterjet cutters can cut virtually any material up to the Z-height of the cutting head, however, thicker materials will cut more slowly than thinner materials. Generally speaking, waterjets can cut through 12 inches of most materials, however, waterjet cutting is usually used on materials 3 inches thick or less.
Precision and Accuracy – Waterjet cutters can maintain precision for nearly any material with an exceedingly small margin of error. The ability to meet tight tolerances ensures manufacturers continuously comply with the rigorous regulatory standards commonly found in the aerospace, automotive, and medical industries. Waterjet cutters like the OMAX 60120 JetMachining® Center can maintain tight cutting tolerances (+/-.005″) for sheets of steel, metal, or plastic at various thicknesses.
Cutting Speed – Waterjet cutting tables cut 5-10 times faster than wire electrical discharge machining (EDM) when cutting material less than 1 inch thick, but generally not as fast as plasma and laser cutters. Waterjet cutting speed is affected by several factors including material type, thickness, and desired edge quality. Compared to other competitive abrasive waterjet cutters in the industry, the OMAX 60120 JetMachining® Center has the fastest cutting speed at 350 in/min (8,890 mm/min).
Reliability – The highly robust and reliable waterjet pump design is capable of operating over 1,000 hours between maintenance.
Value-Added Software – Advanced waterjet cutters are equipped with value-added software and technology designed to meet and exceed the evolving precision cutting needs of manufacturers. Here are some of the exclusive proprietary technologies that come with the OMAX 60120 JetMachining® Center.
- Standard IntelliVISOR SE System Monitoring offers predictive maintenance and system monitoring to minimize unexpected downtime and increase efficiency.
- The exclusive EnduroMAX pump delivers faster and more efficient custom cutting. The pump has the highest nozzle horsepower in the industry.
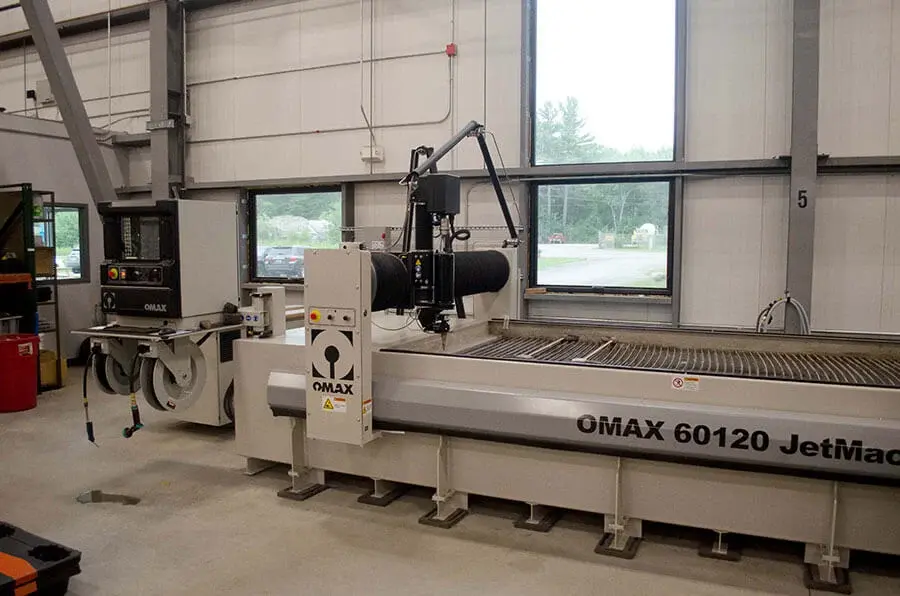
{{cta(‘8467a438-0a2e-416a-a307-c6ef9880c9dc’)}}
Automated Static Cutting Tables
While waterjet cutting excels at cutting metals and thicker materials, automated static cutting tables are fabric-based and excel at single to low-ply cutting. OEMs and businesses that need to cut complex shapes for smaller production runs can avoid die cutting and custom die by leveraging automated static cutting tables.
Here are the characteristics and advantages associated with automated static cutting tables.
Materials – The Eastman M9000 static cutting table can cut sheets of fabrics up to 8 feet wide and 20 feet long and is capable of cutting materials including but not limited to cheesecloth, plastic, cotton, leather, nylon, and vinyl as well as more high-tech materials such as carbon fiber, p-tex, and fiberglass-polyester blends.
Thickness – Automated static cutting tables can cut thin layer films at a quarter-inch thickness.
Precision and Accuracy – Automated static cutting tables are capable of maintaining mid-range cutting tolerances (+/-.030″) for rolls of fabric at a quarter-inch thickness or less.
Cutting Speed – The Eastman M9000 static cutting table can accurately cut virtually any flexible fabric at speeds up to 60 inches per second (152.4 cm/second).
Reliability – The Eastman M9000 static cutting table maintains reliability for 2,000+ hours of normal operation use.
Value-Added Software – Advanced automated static cutting tables have several software add-on capabilities that enable manufacturers to accomplish their tasks quickly and with better results. Eastman’s operating control software, cutPRO, is a user-friendly, all-inclusive platform that makes it easier to import files in various formats, manage cut speeds, accelerations, and tool types per material requirements.
Partnering with a Contract Manufacturer with Diverse Precision Cutting Capabilities
Advanced precision cutting tables including waterjet cutters and automated static cutting tables provide OEMs and businesses a complementary and versatile cutting solution with superior advantages over traditional manual cutting processes.
By understanding the unique advantages of each cutting table, OEMs and businesses can choose a contract cutting partner that has the equipment and cutting capabilities that best fits their order capacity and unique cutting requirements. Before cutting into your bottom line, discuss your precision cutting project with an experienced contract manufacturer to ensure your materials are cut with the custom cutting method best suited for your production run.