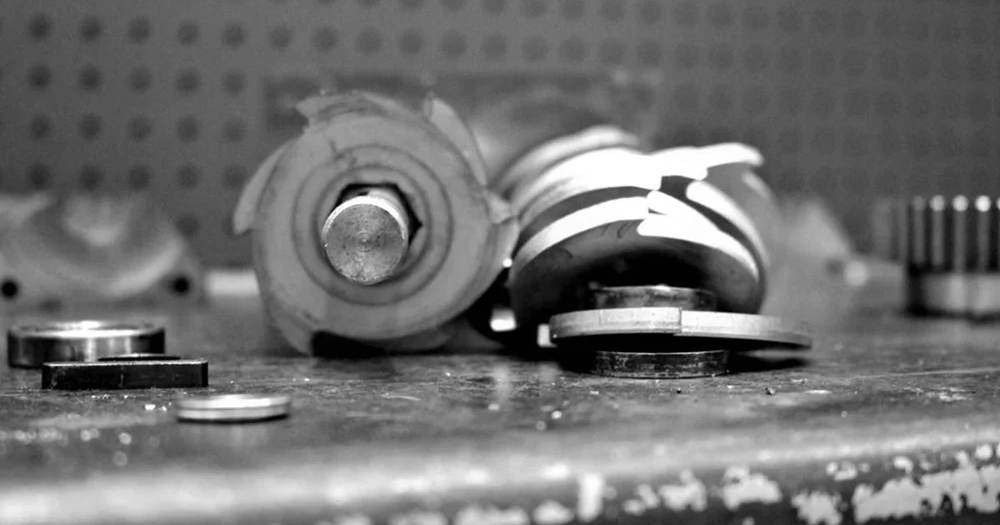
Whether you’re a manufacturer limited on time or a business adhering to a tight budget, selecting the best-suited metal finishing method is complex as there are various factors to consider including material properties, speed of production, and budgetary restrictions.
Here are some factors and questions manufacturers and businesses should consider when selecting a metal finishing process for their manufacturing project.
3 Factors to Consider When Choosing a Metal Finishing Process
Metal processing and finishing services provide a durable, easy-to-clean, and aesthetically-pleasing finished product that exceeds customer expectations. There are numerous types of metal finishing processes, each offering unique advantages. It is highly recommended to review the various types of metal finishes to help narrow down the choices best suited to your manufacturing project.
Once manufacturers and businesses evaluate the types of metal finishing processes and consolidate their choices, they should consider the following factors before making a final decision.
Material Properties
To ensure optimal product performance, it is essential to consider the material’s defining properties such as hardness. Stronger metal products and components require a more intense metal finishing style, such as abrasive blasting to provide a visible finish.
Here are some other material properties to consider when choosing a metal finishing process.
Corrosion Resistance – Defined as the capacity to withstand damage caused by oxidation or other chemical reactions that would otherwise occur when the material is exposed to a given environment. Stainless steel and aluminum metal have high corrosion resistance, whereas carbon steel is less resistant to corrosion.
Machinability – Defined as the ease with which a metal can be cut or shaped while providing a satisfactory surface finish. Materials with low machinability expedite cutting tool degradation and require more power to cut, therefore resulting in a more expensive process. Materials with good machinability require less energy and cut quicker. Stainless steel is hard to machine, whereas steel has medium machinability.
Ductility – Ductility indicates material malleability and refers to a material’s ability to be drawn or plastically deformed without losing strength or breaking. For example, a material like stainless steel has high ductility, whereas aluminum has low ductility.
Weldability – Weldability measures how easily a material can be welded with similar materials without cracks and degradation. Stainless steel has medium weldability, whereas steel is easily weldable.
Tensile Strength – Measured in units of force per cross-sectional area, tensile strength is the load or amount of stress that a material can handle before it stretches and fractures. Measuring a metal product’s ability to withstand failure under mechanical loads is integral for successful structural engineering applications. Aluminum and zinc have relatively low tensile strength, whereas tungsten and stainless steel have high tensile strength.
Here are some questions to consider when analyzing a material’s properties for metal finishing:
- Is the metal finishing type suitable for your project’s materials?
- How much force is required to break the metal?
- How hard is the metal part or product?
- How pliable is the metal part or product?
- How easy is it to solder the metal?
- How easy is it to cut the material using a machining tool?
Speed of Production
Manufacturers and businesses need to maintain supply chain productivity to ensure production requirements and customer demands are met. Therefore, it is crucial to factor in production time when choosing a metal finishing type as some processes take longer than others. If a manufacturer needs to maintain a short turnaround time, they should consider a short metal finishing process.
Here are some questions to consider when analyzing the speed of production for metal finishing:
- Does your manufacturing project have strict deadlines?
- How soon do you want your product to be ready?
- What is the metal finishing processing cycle time?
- Does the metal finishing technique provide the production speed required to meet customer demand?
Metal Finishing Process Cost
Each metal finishing process varies in cost. Some finishing methods like anodizing are costlier than others, but they compensate by providing several advantages including higher quality and faster results. It is essential to evaluate the average cost of each method and only select a finishing option that aligns with budgetary requirements. Be sure to ask the contract manufacturer plenty of questions regarding the specific costs of each metal finishing process to ensure an informed decision.
Here are some questions to consider when analyzing the cost of a metal finished method:
- What is your budget for metal finishing?
- How expensive or inexpensive is the material?
- Is the metal finishing process considered to be cost-effective for your project?
- Is there another metal finishing method that provides similar results at a different cost?
- Does the chosen metal finishing process require preparation and advanced welding tools, thereby increasing overall project costs?
Selecting a Metal Finishing Process for Your Manufacturing Project
Choosing the ideal metal finishing method for your manufacturing project is a complex process. While having a knowledge base of the different types of metal finishes and the main factors to consider is beneficial, consulting an experienced contract metal finishing service provider is recommended.
Manufacturers and businesses should partner with experienced metal processing specialists for assistance in selecting a cost-effective metal finishing method that accounts for specific project parameters and requirements, including material properties, speed of production, and cost. Contract metal finishing services enable manufacturers and businesses to expand their operations without locating extra space or hiring additional employees.